Description
VRP – Silver-Halide photoplates
VRP photographic plates are a practical replacement for Agfa (Millimask) and Kodak (HR-P, TE) plates.
The plates are specifically designed for the manufacturing of high-precision photographic masks for microelectronics. The material is also used for Bragg diffraction X-ray tomography and radiography in many European Synchrotron facilities. High resolution, high durability and excellent adhesion of the emulsion layer to the glass substrate enable photographic features of less than 2.5 micrometers to be recorded.
All photo-plates are usually supplied in a cardboard package containing 6 units each. The largest plate size available as a standard size is 406×300 mm. The standard glass thickness is 2.5 mm. All plates come with an anti-halation coating. Custom glass sizes and film substrates are available for any emulsion on request. Guaranteed lifetime – 12 months.
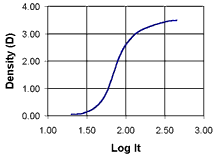
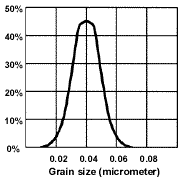
VRP characteristics | |
Average sensitivity, ISO Negative process: Reversal Process: | 0.02 0.04 |
Contrast, not less than: | 5 |
Max. Density, not less than: | 3 |
Spectral sensitization maximum, nm: | 525 |
Spectral sensitization region, nm: | 400-565 |
Fog Density, not more than: | 0.02 |
Resolving Power, mm-1, not less than: | 3,000 |
Strength of emulsion layer after processing, kg force, not less than: | 0.9 |
Temperature of emulsion layer deformation, oC, not less than: | 55 |
Processing and Handling Recommendations
Unseal and process in indirect non-actinic light with use of a dark-green light filter (transmission zone – 530 nm and less). Temperature of processing solutions – 20±2°C. Storage condition: Humidity 65% and 12-15deg. Celsius.
Recommended processing for VRP materials for the masks production | ||
Negative process | Temperature of solutions | |
Exposure | ||
Developing | Concentrated VRP developer diluted in distilled water 1:5,4-5min |
20
|
Wash | Rinsing water 3 min |
17±2
|
Fixing | Fixer , 5-10 min |
20
|
Wash | Water 3 min |
17±2
|
Final Wash | Water with wetting agent (Agepon) 1min |
17±2
|
Drying | Slow Air |
20±4
|
Reversal process
|
||
Exposure | ||
Developing | Concentrated VRP developer diluted in distilled water 1:1.7, 4-5min |
20
|
Wash | Rinsing water, 3 min |
17±2
|
Bleaching | Bleach , 1.5 min |
20
|
Wash | Rinsing water, 3 min |
17±2
|
Brightening | Brightener , 3 min |
20
|
Wash | Rinsing water, 5 min |
17±2
|
Lighting | 500 W lamp, 70cm distance from the emulsion, 1 min | |
Second Developing | Concentrated VRP developer diluted in distilled water 1:5 – 3 minutes |
20
|
Wash | Rinsing water, 1 min |
17±2
|
Fixing | Fixer , 2 min |
20±4
|
Wash | Rinsing water, 3 min |
17±2
|
Final wash | Water with wetting agent (Agepon) 1min |
17±2
|
Drying | Slow Air |
20±4
|
VRP Material Processing Scheme used in X-ray Tomography and Radiography
|
||
Procedure |
Chemicals
|
Temperature
|
Exposure | ||
Developing | Kodak RP X-OMAT Developer , 5min |
20
|
Wash | 2min |
17±2
|
Fixing | Kodak RP X-OMAT LO Fixer , 5min |
20
|
Wash | Water, 10 min |
17±2
|
Drying | Slow Air |
20±4
|